Sustainability within Natpak & Alpha Packaging
Natpak is one of Zimbabwe’s key packaging manufacturers, who uses state of the art technology and equipment in their manufacturing processes at three factories in Harare.
Various sizes of Polyethylene terephthalate (PET) pre-forms, High Density Polythene (HDPE) bottles and closures for the packaging of beverage, dairy and chemical products are produced at the Rigids division factory. Woven sacks used, for example, for maize meal, stock feed, grain, seed or fertiliser packaging, are produced at the Sacks factory. The Flexibles factory focuses on primary food packaging such as pouches used in poultry packaging, bread bags, FFS sheeting used in sugar, rice, salt, milk, snacks and treats packaging as well as secondary packaging such as shrink and stretch wrap film, baler bags and black sheeting. The printing of the plastic packaging of many of Zimbabwe’s iconic brands takes place at both the Flexibles and Sacks factories, using advanced printing presses.
Natpak also has a corrugated box and egg tray manufacturing division, Alpha Packaging.
The product range includes corrugated boxes, tobacco cartons, egg trays, paper bags and folding cartons. Any off-cuts from the main production process are recycled and used to produce the egg trays. The company also recycles waste from third parties, such as Lotus Stationery, for the production of the egg trays.
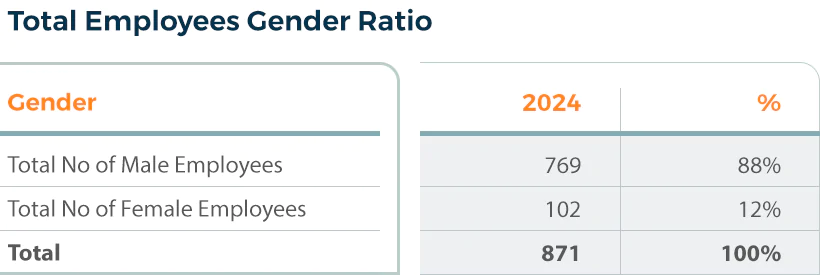
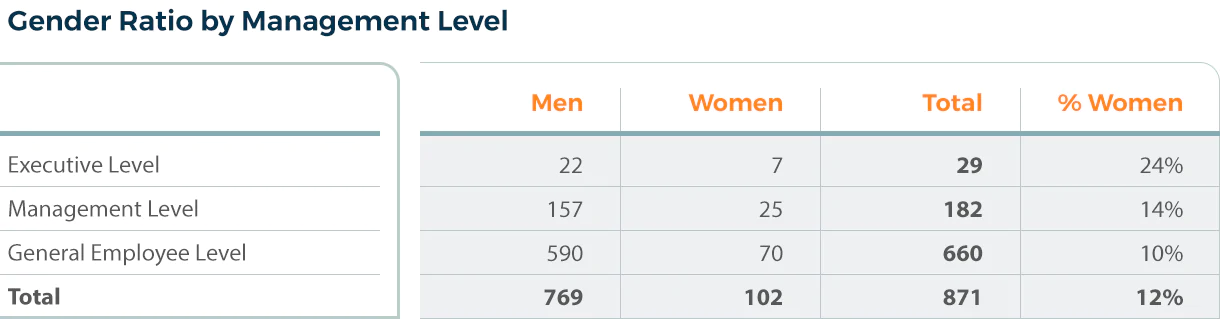
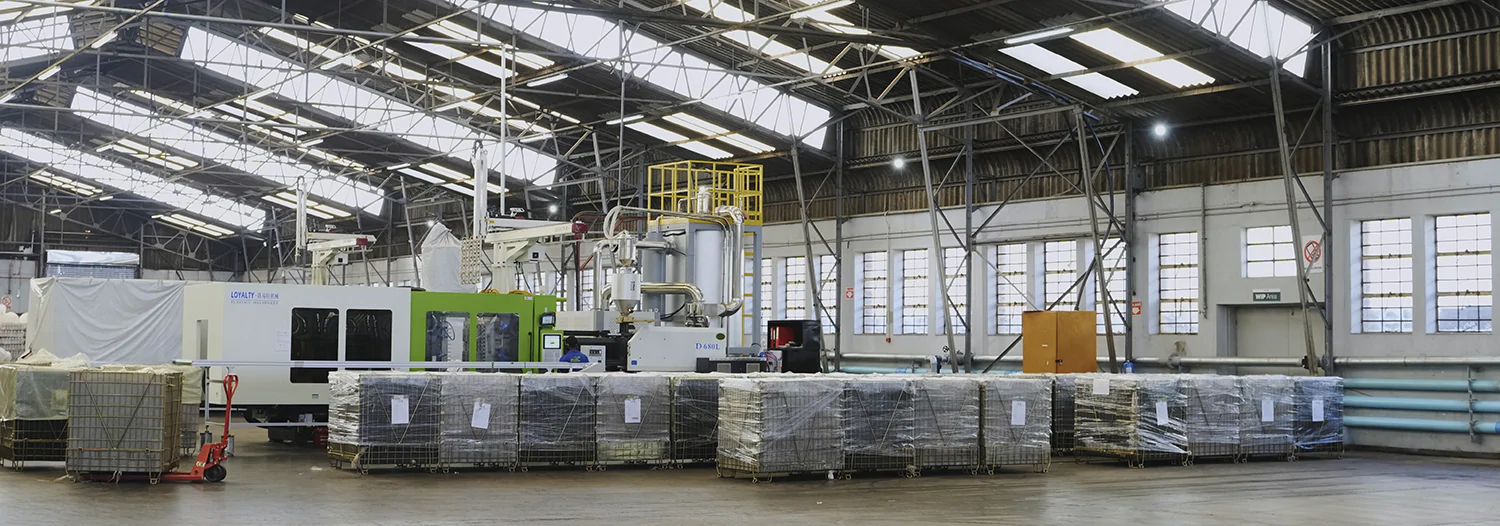
During F2024, 655 female casual staff were employed in the reporting year by the Sacks division as sewing machinists to stitch sacks.
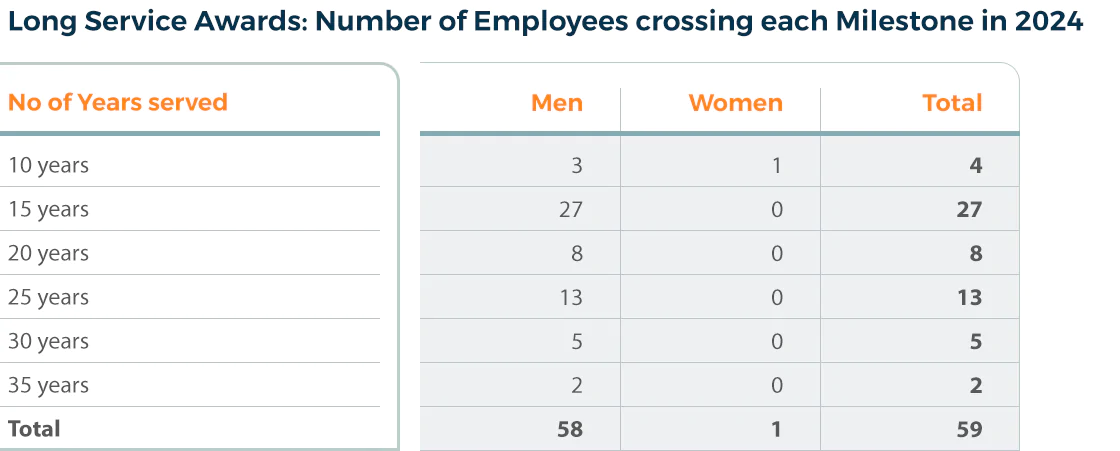
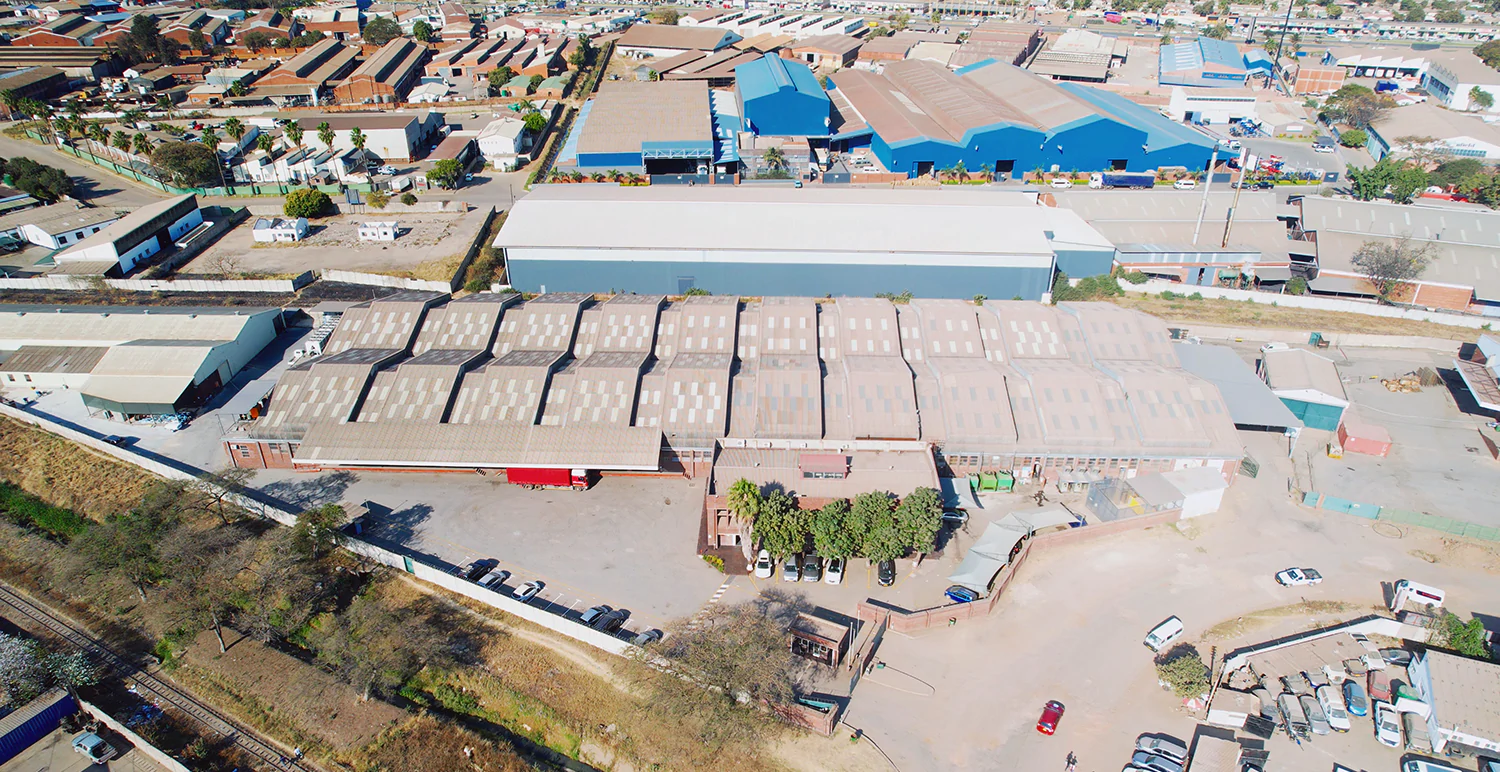
Key Sustainability Highlights
- Natpak’s three plastics divisions have been certified to Global Standard (BRCGS) for Packaging Materials in 2022. As a result of the audit that took place during F2023, Natpak’s certification was upgraded from B to AA rating. Due to an unannounced audit in F2024, Natpak was further upgraded to the commendable AA* rating. BRCGS is the Global Food Safety Initiative (GFSI) benchmarked certification which gives customers assurance on product safety, quality, authenticity and legality
- Natpak’s Flexibles division became SMETA certified which is a prerequisite requirement for trading with Nestle. SMETA is a social compliance audit focusing on Safety, Health, Environment Management, Human Rights and Ethics. Natpak’s Rigids division has renewed its Coca-Cola supplier requirement, SGP (Supplier Guiding Principles) certification.
- This year seven electric forklifts have been commissioned which has resulted in cleaner operations and improved air quality in the warehouse. The forklifts are charged at night during off-peak, low demand periods reducing the pressure on power requirements and costs.
- Additional energy efficiencies have been targeted through the installation of a variety of new and improved machinery.
- Natpak is a member of the Zimbabwe Recyclers Association as a way of partnering with fellow recyclers.
- Natpak implemented and strengthened its plastic waste management system. The recycling plant has improved output capacity and has upgraded its recycling plant by installing a new pelletiser, vibrator and drier to improve the efficiency of the plant and quality of the final products. Industrial plastic waste, both internal and external, is recycled into pellets. These are for internal use in the production of black sheeting and also sold to other players in the industry. During F2024, 831.6 tonnes of recyclable waste was recycled at the plant compared to 774 tonnes in F2023.
Alpha Packaging
- Alpha Packaging has enhanced energy efficiencies by improving machine speeds through efficient steam reticulation and improved coal usage per ton produced.
- Alpha Packaging is in the process of installing a laboratory for the Quality Assurance department.
- Egg trays are produced from 100% recycled paper. During F2024 Alpha Packaging used 07 tonnes of recycled paper for its egg tray production.
- With a zero-waste philosophy, recyclable paper waste is used for egg tray production and any excess is sold to Baobab Papers who recycle this into brown paper that Alpha in turn purchases for some of its corrugated products.
- Solar power continues to supply the offices, reducing Alpha Packaging’s reliance on diesel run generators during power outages.
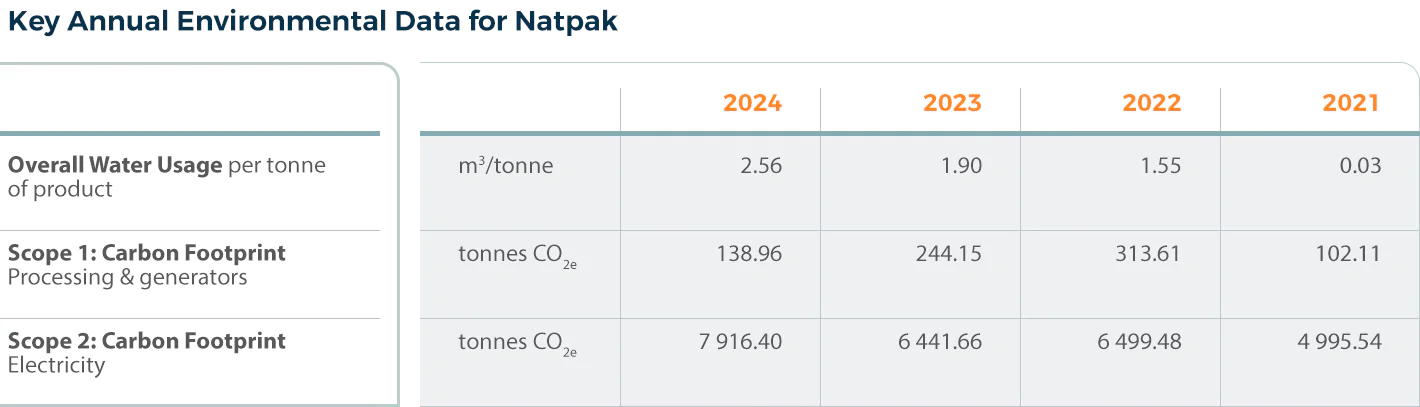
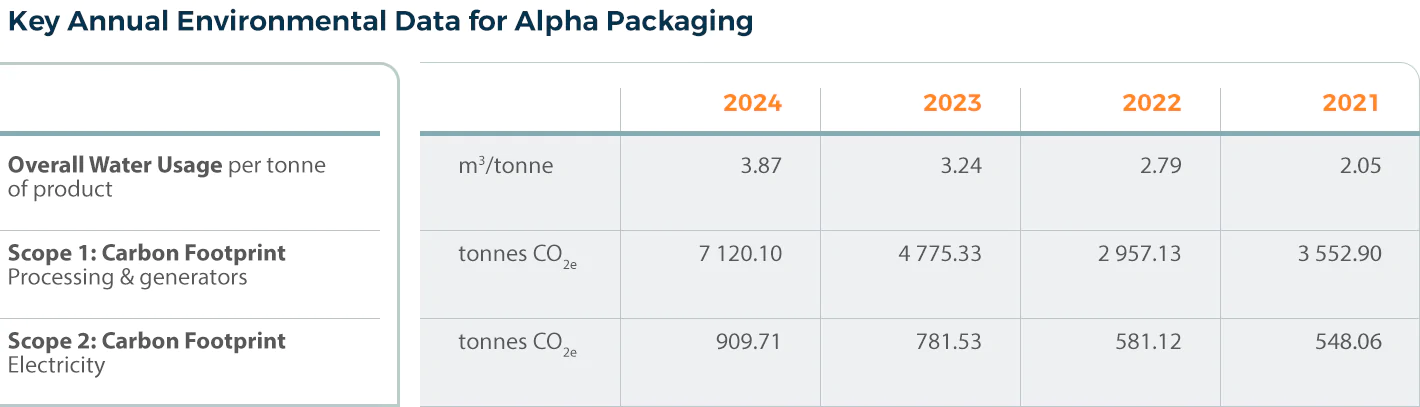
Note:
- For the historical data to be comparable, the Scope 1 Carbon Footprint for 2021 to 2023 has been recalculated using the Department for Environment, Food and Rural Affairs (UK) (DEFRA) factors for 2024.
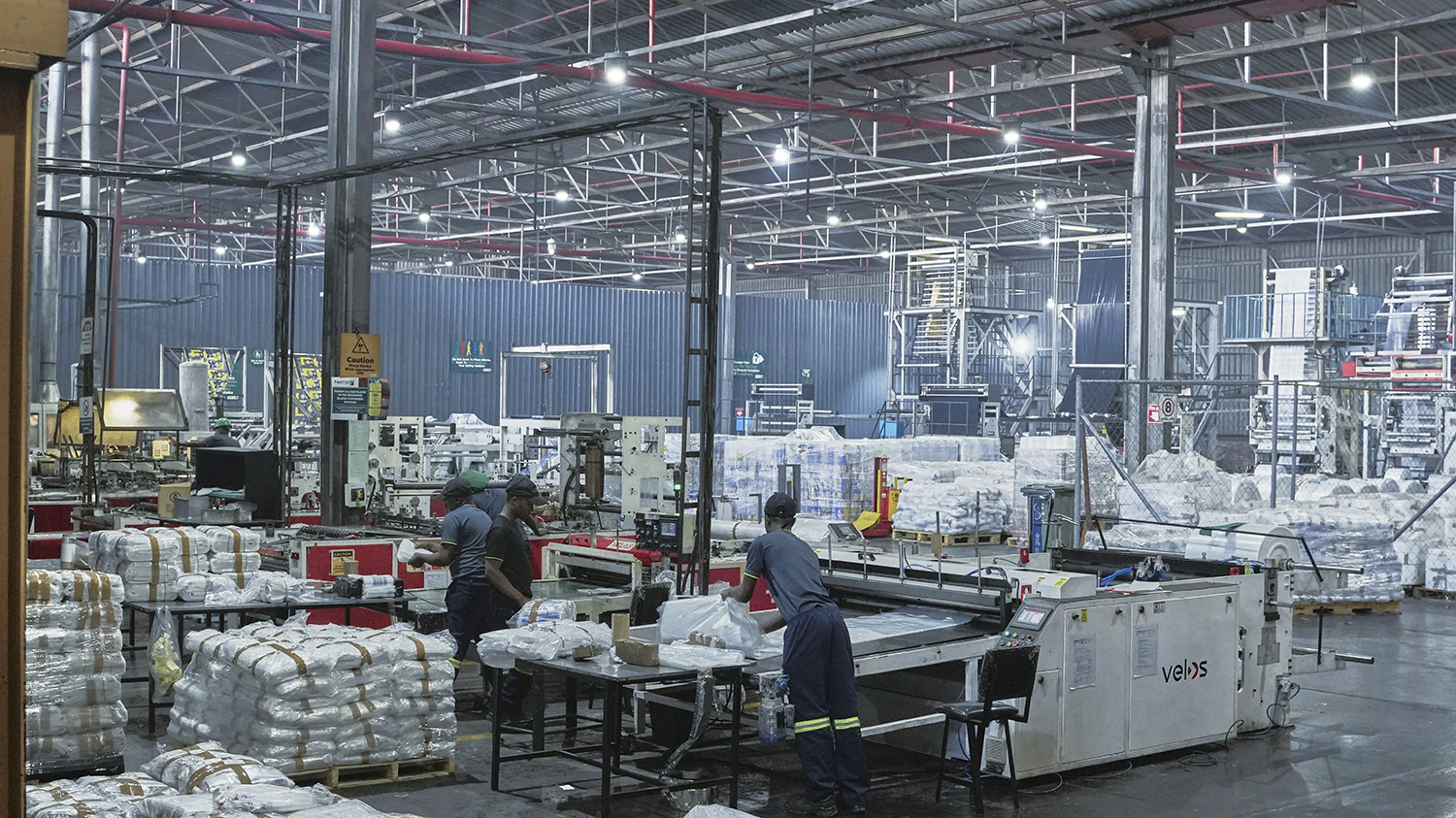